Sustainable Operations
Driving to net zero in our plants and operations.
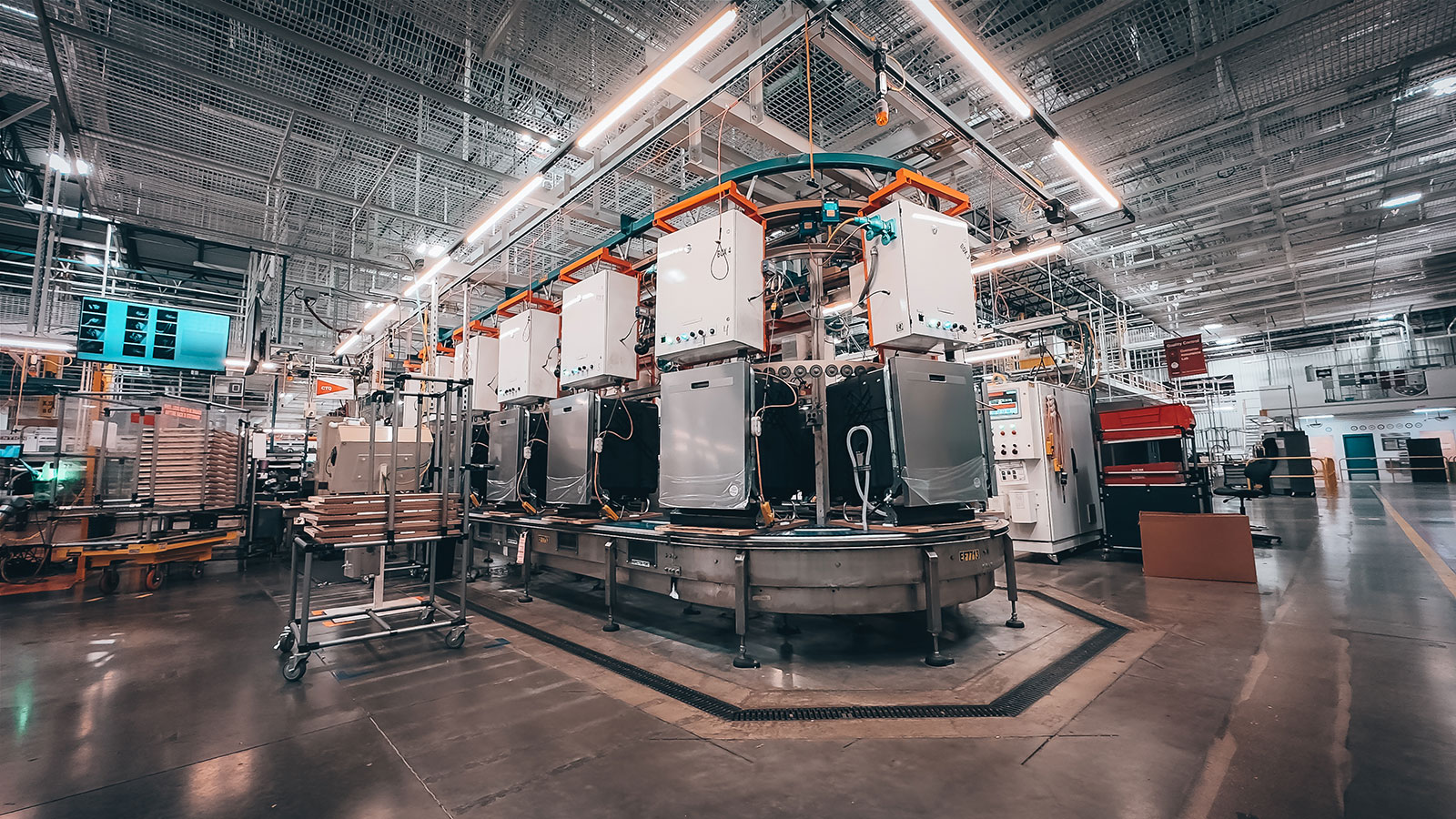
Greenhouse Gas (GHG) Emissions (scopes 1 and 2)
In 2003, Whirlpool Corporation was the first appliance manufacturer to set an emissions reduction target, and we are on track to achieve our commitment of Net Zero emissions in our plants and operations by 2030. This commitment covers all large manufacturing sites and distribution centers around the world, spanning all identified direct (Scope 1) and power-related (Scope 2) emissions.
Our Commitment to Achieve Net Zero Emissions Target in Plants and Operations
Our Plan to Reduce GHG Emissions
REDUCE
ENERGY USE
Reduce energy consumption through both WCM efficiency projects and facility retrofits. Projects include LED lighting, compressed air use reductions, and boiler and HVAC optimization.
EXPAND
RENEWABLES
Implement 100% renewable energy for electricity consumption.
ELECTRIFY/
SUBSTITUTE
Electrify and substitute fossil fuels (with hydrogen, bio-gas or other) everywhere possible to reduce scope 1 emissions.
CARBON OFFSET
CREDITS
If necessary, invest in high-quality carbon removal projects and any other carbon credits to offset unavoidable emissions.
Driving to Net Zero Emissions in Our Plants and Operations
36%
In 2024, we reduced scopes 1 and 2 market-based emissions by 36%* compared to 2023.
third consecutive year
2024 is the third consecutive year we’ve achieved double-digit emissions reduction.
*The 36% reduction includes 18% from the divestiture of the EMEA region and 18% from focused projects.
Market Based Emissions
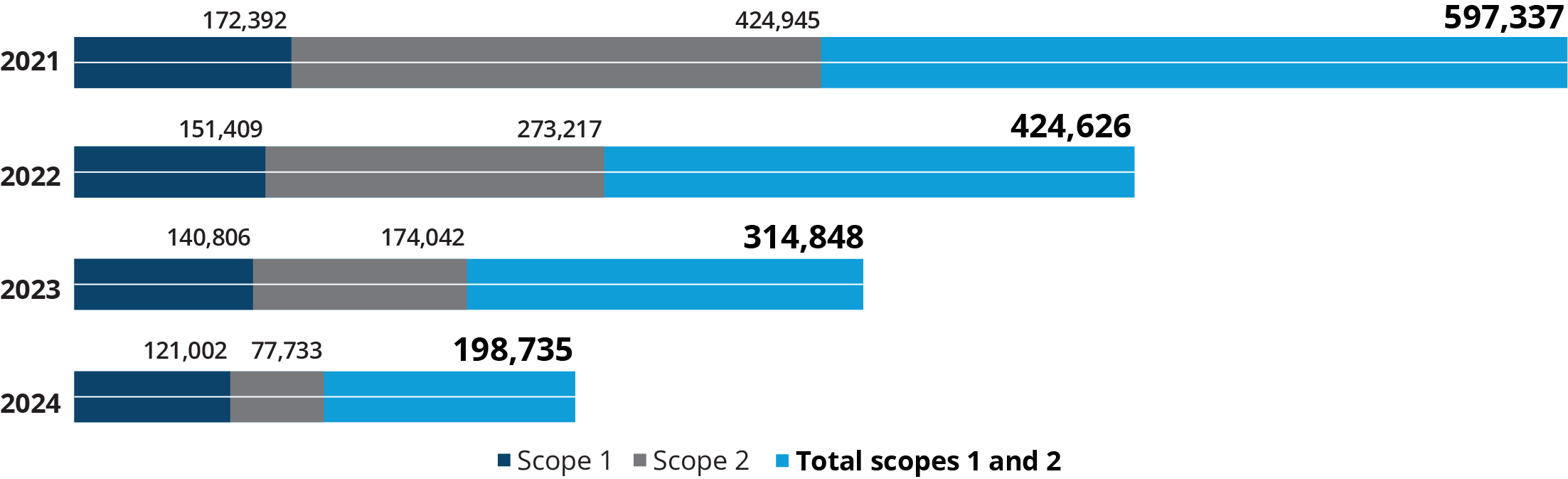
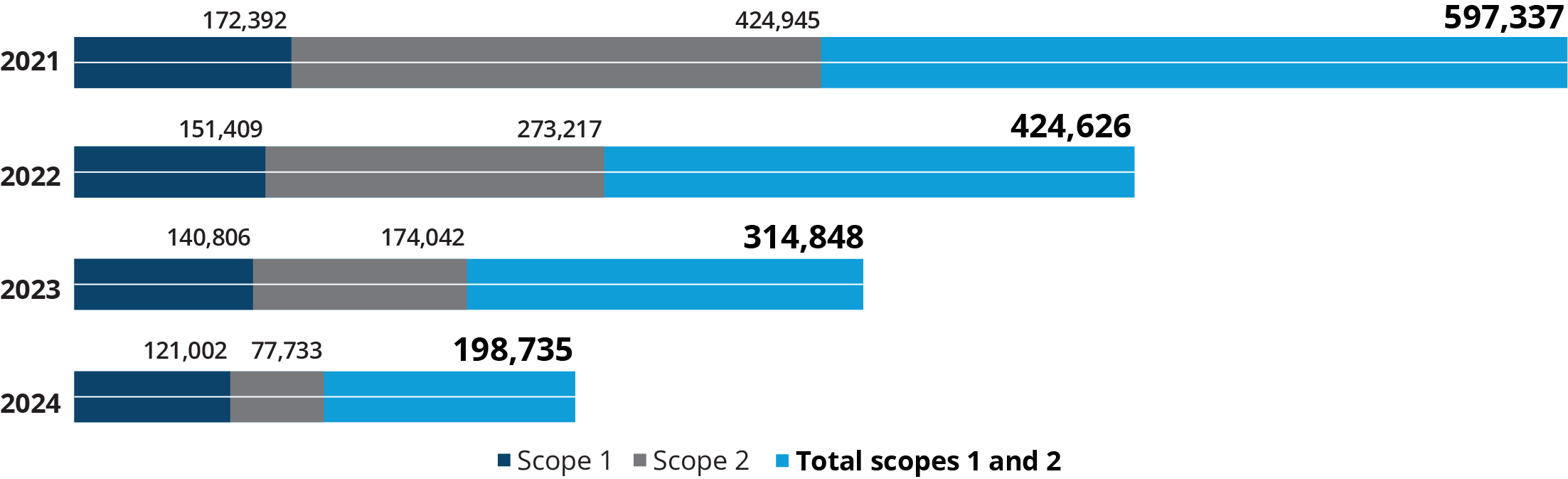
See our latest Sustainability Report for more on our efforts to reduce Scope 1 and 2 emissions and our Sustainable Products page for Scope 3 emissions information.
Resource Management
We know our ability to operate in the future depends on continuing our commitment to produce products with purposeful innovation, without leaving a negative footprint, while helping protect the planet, our employees and the communities where we live and work. We ensure a high standard of sustainable operations across our many types of workplaces through a set of management systems and standards:
World Class Manufacturing (WCM)
WCM is our system for improving productivity, quality and reducing waste and losses across the company through committed employee involvement and rigorous application of methods and tools.
SAFETY
COST
DEPLOYMENT
FOCUSED
IMPROVEMENT
AUTONOMOUS
MAINTENANCE
WORKPLACE
ORGANIZATION
PROFESSIONAL
MAINTENANCE
QUALITY
CONTROL
LOGISTICS &
CUSTOMER SERVICE
EARLY EQUIPMENT
MANAGEMENT
PEOPLE
DEVELOPMENT
ENVIRONMENT
We Care Commitments
“We Care” Environment, Health, Safety, Sustainability (EHSS) Management System is the operating framework that helps ensure a workplace that protects our people, preserves the environment and enables the business and our people to act sustainably. These commitments are the shared responsibility of every Whirlpool employee.
Key Resource Management Efforts
Whirlpool is making investments in alternative sources of energy, including significant wind energy projects. In 2024, we are matching 100% of our electric energy consumption from on-site systems in the U.S. manufacturing sites combined with renewable energy credits from two off-site renewable energy projects. Read more in our latest sustainability report.
We continue to increase solar energy production and use our operations around the globe, further supporting our goal to increase reliance on renewable energy. Read more in our latest sustainability report.
We are expanding our purchase of renewable energy credits to match our energy usage in certain sites around the globe. Read more in our latest sustainability report.
By adding water meters to select sites, we gained insights used to calculate and then streamline water efficiency projects. Some sites also recirculate water after treatment at the wastewater treatment plant. Read more in our latest sustainability report.
We first set the goal to reach ZWtL in 2012, and since then we have been on a journey to invest in plant efficiency, waste reduction, recycling and other efforts to eliminate waste in our operations and contribute to a circular economy. In 2024, we achieved a 97% or higher landfill diversion rate in all our global manufacturing sites (above ZWtL Gold status level, which requires a minimum of 95% diversion from landfill). Read more in our latest sustainability report.